What are the relevant questions to ask when considering the purchase of the most economical cushioning solution ?
You are a logistician, craftsman and/or e-merchant and you want to optimise your packaging costs as much as possible while ensuring the protection of your creations, products or those of your customers within the parcel.
To go beyond a simple packaging purchase price reflex, you need to broaden your thinking and take other factors into account by asking yourself a number of key questions :
The list is not exhaustive, but is intended to structure the various points to be studied. Of course, there is no such thing as a perfect set-up, but one that is adapted to each situation and to your specific needs.
1/Compare purchase prices per m3
This is a good place to start, as it has a decisive impact.
To make the right comparison, it is essential to use the same criteria, and the one to be recommended, because we are talking about cushioning volume, is of course the m3. The containers are sometimes different: 0.4 or 0.5m3 particulate bags versus 1m3 or 2m3 compressed bags, or kraft paper that has to be crumpled. So be sure to compare the price per cubic metre of each of the solutions on offer.
2/ Calculate your consumption
You may have paid a good price for your cushioning, but if it’s not suitable, it can lead to over-consumption, which can be detrimental in the end.
Several standard test parcels with different cushioning solutions will enable you to calculate your average consumption per parcel and deduce the average cost of your cushioning per parcel.
Then all you have to do is extrapolate :
Price per m3 x actual consumption x number of cartons shipped.
3/ Consider storage requirements and footprint
How much space will your cushioning stock take up?
The minimum order and the necessary permanent stock will affect your cash flow. All fixed stock has a value and must therefore be optimised from both a financial and a physical point of view.
Any space taken up by storage can mean less sales space and/or a loss of operational efficiency. If you’re a logistics specialist, your core business is optimising locations, so this criterion should be taken into account.
How many spaces (pallet surface 80×120) will I need and what stock value will be considered ?
- A bag of dunnage particles (0.5 or 0.4 m3), for example, will require more space than goods in rolls or compressed bags.
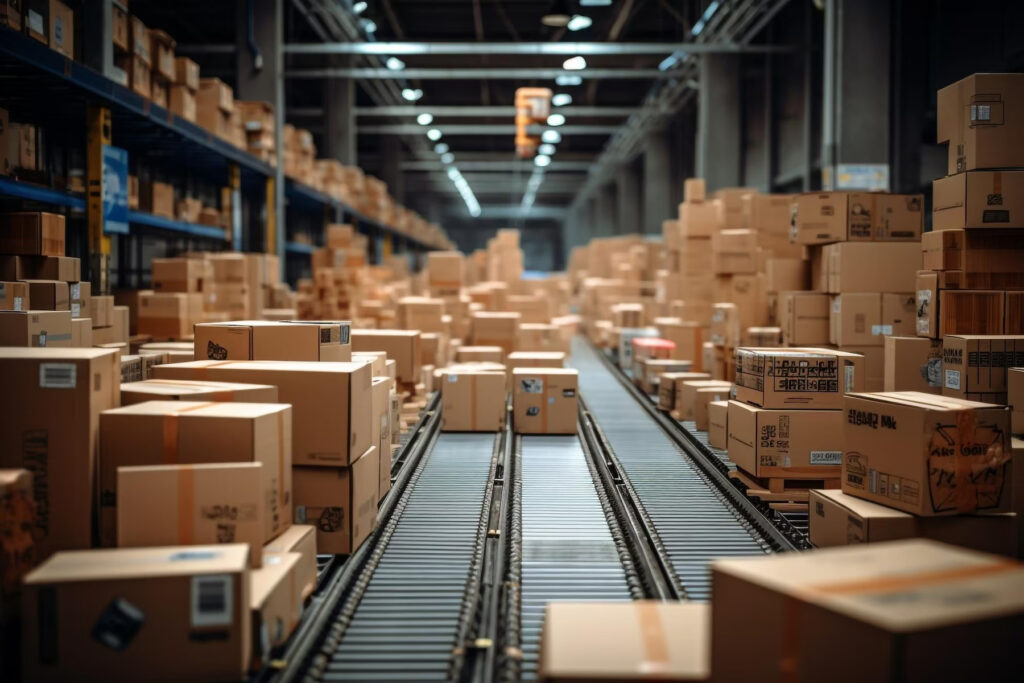
4/ Think about transport costs and reduce empty space
For transport, 2 key criteria must be considered :
- The volume
- Weight
Your cushioning must be efficient and therefore enable you to protect while optimising the size and therefore the cost of your boxes. Not to mention the customer dissatisfaction of receiving too large a box and the cost to the planet.
We’ve all ordered something from an e-commerce site and received it in a parcel that was out of all proportion to the size of the item.
To illustrate this, see our previous article here : https://www.blocbox.fr/la-nature-a-horreur-du-vide-et-elle-nest-pas-la-seule/
Some customers of the Blocbox textile cushioning solution, for example, have been able to reduce the size of their cardboard boxes because the expanding wadding limits the void while providing good protection.
Most transport companies use weight/volume calculations.
To find out more about calculating weight/volume : https://www.aunismessagerie.com/tout-savoir-poids-volumetrique-marchandise-transport/#:~:text=Par%20exemple%2C%20si%20votre%20colis,kg%2Fm3%20%3D%204.
It is therefore essential to master this aspect in order to make substantial savings.
Companies like Colisconsult, for example, can help you think about this and optimise what can be done, including, of course, negotiations with carriers.
To find out more about Colisconsult : https://www.colisconsult.com
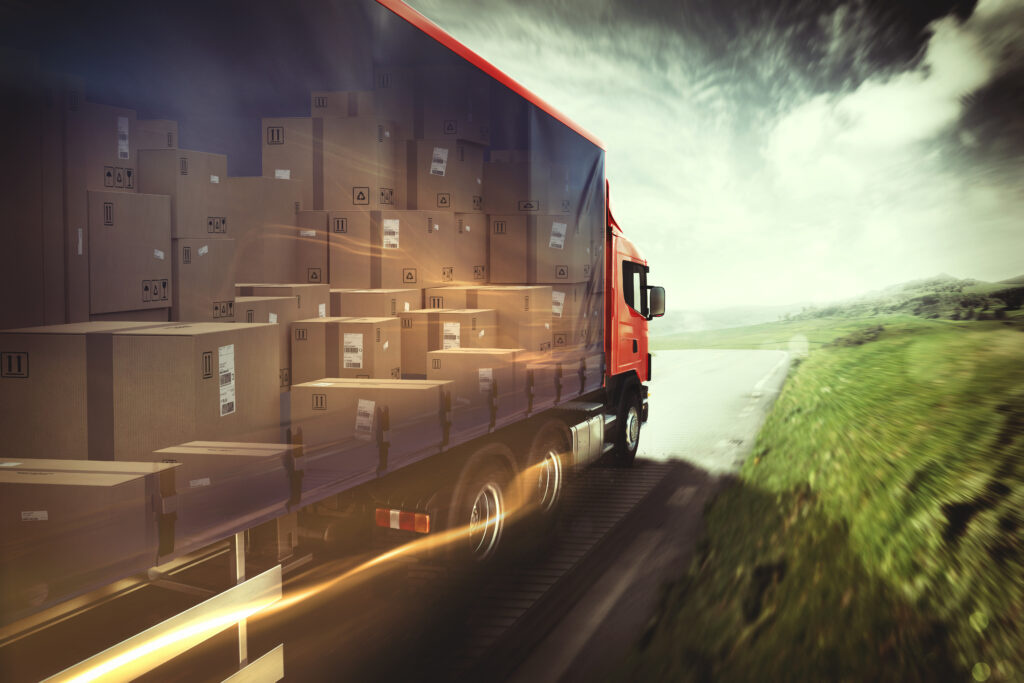
5/ Keep disputes to a minimum
And yes! We sometimes tend to forget that the primary function of packaging is to protect. Wedging prevents movement, shocks and vibrations.
Uncontrolled protection means more disputes, and more disputes mean more costly consequences :
There’s nothing more puzzling than finding a beautiful ceramic lamp in pieces when you receive your parcel.
A high rate of breakage can lead to a number of costs for a company.
1/ Replacement costs (reshipment + reimbursement)
2/ Logistics costs: management and processing of returns, disruption to the supply chain.
3/ Damage the company’s reputation and therefore reduce sales.
Not all solutions are created equal and, above all, they must guarantee good protection.
In certain situations, it is useful to turn to experts who can validate the protective characteristics of a packaging through crash tests.
This is the case, for example, with Protection efficiency®.
To certify the efficiency of a cushioning solution, the Protection Efficiency® was created to meet very demanding specifications for testing the resilience and impact protection properties of a cushioning material. These tests reproduce the stresses experienced by a parcel during transport and delivery.
To find out more, click here : https://www.agencephotosynthese.com/labelliser-vos-emballages/
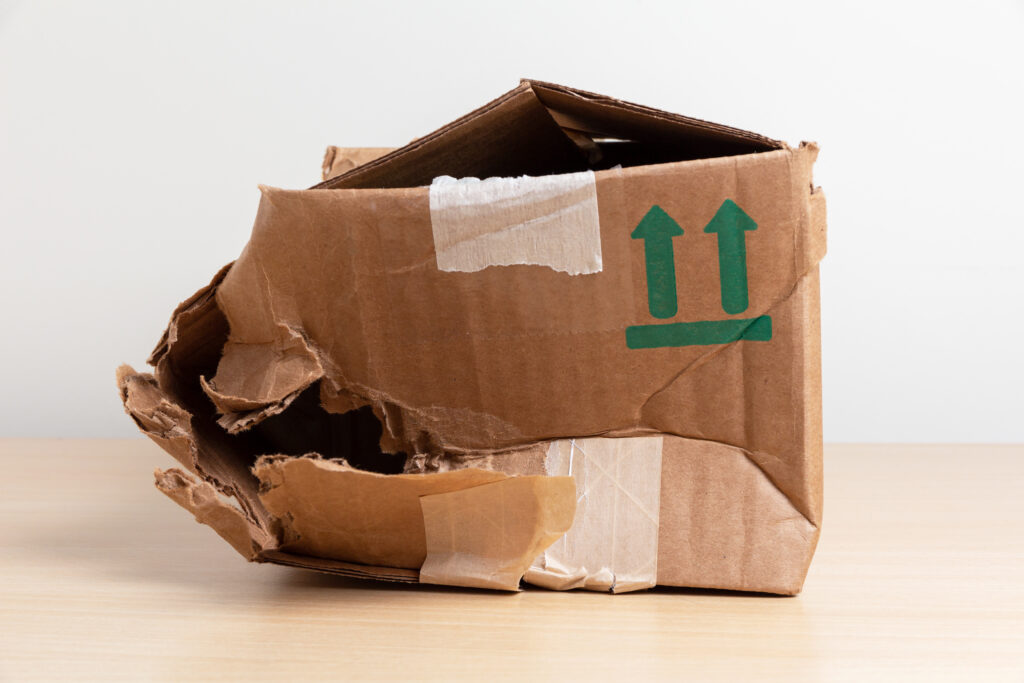
6/ Optimise preparation time and costs
How long does it take the operator to pack the product correctly? Will he have to use several different cushions (e.g. bubble wrap + kraft paper) or, in other words, how many different operations will he have to carry out ?
By asking yourself these questions, you can better assess the advantages and disadvantages of the layout you are considering, while also taking into account the logistical aspects.
To reduce labour costs in the packaging process, it can be advantageous to choose easy-to-use cushioning solutions. This allows operators to quickly acquire the necessary skills while maintaining a high work rate, thus avoiding a significant loss of time and money in the training process.
There are other factors that help to reduce labour costs, such as the distributors of dunnage solutions. There are several types in the logistics sector. These dispensers facilitate the packaging process by supplying the necessary cushioning materials quickly and efficiently.
The choice of dispenser often depends on the type of cushioning material used and the company’s specific packaging requirements.
The Logistibox dispenser for cushioning solutions made from recycled textile wadding is also designed to reduce operators’ MSD, as is the crumpled paper machine, which crumples kraft paper directly so that the operator doesn’t have to.
To find out more about Logistibox : https://www.blocbox.fr/distributeur-inox/
In short, you’ve understood that a choice of cushioning can’t be improvised. It pays to take the time to study these 6 aspects. The savings are substantial, both for your company and for the planet !